CBM is often employed in industries where equipment downtime can have significant financial and operational consequences. It requires a combination of technology, data analysis, and maintenance expertise to implement effectively. Instead of performing maintenance tasks on a fixed schedule (e.g., time-based maintenance) or waiting for equipment to fail (breakdown maintenance), CBM relies on data and information gathered from sensors, inspections, and other sources to determine when maintenance is needed. The goal is to perform maintenance activities only when they are necessary, optimising asset reliability, availability, and cost-effectiveness.
Course Description
Duration:
1 day
Example Hours:
Training Day 1: 8.00am to 4.00pm
Format:
Classroom learning
Pre-Study:
Not required.
Outcome:
You will come away from this course with a very good understanding of maintenance types and condition based maintenance techniques and programmes.
Course Includes:
- 1 day classroom training
- Lunch and refreshments
- Short-form booklet
- Certificate of Completion
Course Summary
Monitoring: Continuous or periodic data collection and monitoring of equipment or asset conditions. This can involve various technologies such as sensors, vibration analysis, thermography, oil analysis, ultrasound, and more.
Data Analysis: The collected data is analyzed to assess the current state of the equipment. Patterns, trends, and anomalies are identified to predict potential failures or deterioration.
Decision-Making: Maintenance decisions are based on the analysis of the equipment's condition. When a certain condition threshold or predefined criteria are met, maintenance activities, such as repairs or component replacements, are scheduled.
Predictive Maintenance: CBM can be used for predictive maintenance, where maintenance actions are scheduled just in time to prevent equipment failures, reducing downtime and costly repairs.
Cost Savings: CBM can result in cost savings compared to traditional preventive or reactive maintenance approaches. By addressing issues when they are detected, organizations can avoid unnecessary maintenance and extend the operational life of equipment.
Equipment Reliability: CBM helps improve equipment reliability and availability by proactively addressing potential problems.
Safety: CBM can enhance safety by reducing the likelihood of unexpected equipment failures, which can lead to accidents or injuries.
Register Your Interest
Assess. Align. Perform.
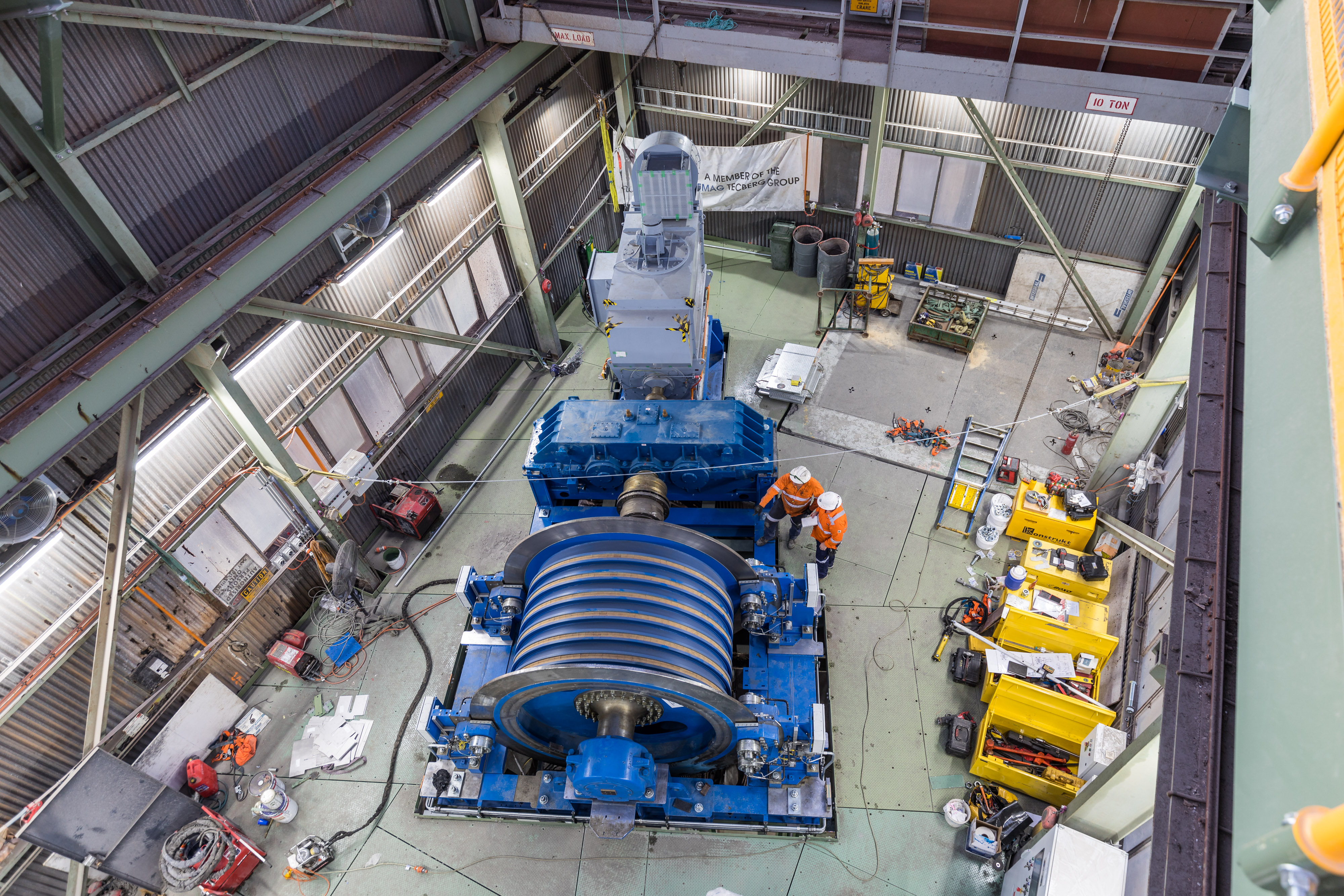